Centrifugal Pump UND/III
ANSI/ASME B73.1 Standard
UND/III process pumps, in addition to fully meeting the specifications of the latest edition of ANSI/ASME B73.1 standard, continue to be improved to offer the user superior equipment, with high efficiency, excellent performance, and a longer Mean Time Between Maintenance (MTBM), guaranteeing them the fair reputation of highly reliable pumps in the most difficult process conditions, making UND/III pumps among the best in their class worldwide.
Operational Parameters
Capacity: ___________________________ up to 1700m3/h
Total manometric head: _____________ up to 210m
Maximum Rotation: ___________________ 3600 RPM
Temperature: __________________________ up to 260ºC (special constructions up to 350ºC)
Project Features
- SUPEROX enlarged seal chamber standard on all UND/III pumps. This system increases the circulation of liquid in the seal chamber and therefore in the mechanical seal, reducing the temperature of the faces while at the same time removing solids through centrifugal action, allowing for better lubrication. The design allows the change from mechanical seal to packing and vice versa in the field and without the need for any additional machining. The fully open seal chamber with conical walls CONEBOX allows the assembly of single or cartridge seals with pressurized circulation or cooling. The SUPEROX or CONEBOX systems allow the adoption of the most varied sealing systems. Single or double cartridge or tandem mechanical seals with options for accessories are accommodated in these seal chambers, which have large dimensions, which also allow for great ease of maintenance.
- Semi-open impeller that efficiently pumps clean or loaded liquids. Optionally, the impeller is supplied with a mechanical locking system, which prevents it from coming loose from the shaft in the event of reverse rotation due to fluid return or motor connection or assembly error.
- Bearings designed for 25,000 hours of useful life, with automatic lubrication by oil mist and in continuous service.
- Shaft with maximum shaft deflection 0.005″ (0.13mm).
- Bearing protectors are standard on bearing supports to prevent solid or liquid contaminants from entering the bearing support.
- Cooling system made by finned tube for water circulation that can be installed as an option on the bearing support.
- Maintain performance with a simple system with just clearance adjustments, resulting in long-term energy savings.
- Lubrication flexibility that allows, in addition to the normal splash system, the adoption of spray or mist lubrication (“oil mist”)
- Adapter between bearing support and housing made of modular cast iron, with mechanical resistance equivalent to that of carbon steel; guaranteeing greater safety.
- Housing, cover, and adapter assembled with tight fit that ensures connectivity of the shaft and seal housing, extending the life of the mechanical seal and bearings.
- The oversized SAE 4340 high-strength steel shaft can reduce nominal deflection (shafts are also available in other materials), thus reducing L3/D4 and increasing the durability of the mechanical seal and bearings.
- Optionally, the double row bearing that supports the axial load of the rotor can be replaced by two single row, angular contact ball bearings, 40° O-ring mounting. This mounting is particularly suitable for processes where the pump mechanically assembly operates with very high loads.
Advantages
- Housing designed to allow removal of the rotating assembly without disassembly (back pull out).
- Suction and discharge connections or the actuator.
- Meets the “X” and “Y” dimensions of ANSI B73.1.
- Designed with corrosion over-thickness to meet ASME B73.1 requirements.
- Meets the loads in the range according to N 16.2.
- Centerline discharge height and working.
- Rotor: Reduced repair costs, minimum hydraulic loads.
- Accelerometer: Added threads for accelerometer positioning (optional).
- Jack Sealings: Standardization for jack protection instead of retainers, increased reliability, increased MTBF, elimination of constant level lubricator, as well as breather and expansion chambers.
- Adjustment of the motor’s axial clearance: External system that, due to the semi-open rotor, maintains the equipment’s high performance, without requiring new or repaired parts.
- Oil sump: Increased oil capacity provides adequate heat transfer, reducing oil temperature. Replacement of cooling chamber with finned tube.
- Seal box: Designed to promote appropriate heat dissipation and lubrication of the mechanical seal faces.
- Suitable for applications with liquids containing solids, air or steam.
Applications
- Chemical industry — in the transfer of various products, corrosive or not, in the loading and unloading of acids, transfer of organic products, in the pumping of products such as sulfur, urea, ammonia, liquefied gases, solvents, monomers, polymers, and other organic or inorganic products.
- Petrochemical and polymer industry — the pumping of aromatics, light hydrocarbons, heat transfer liquids, reflux and bottom of towers, diesel, condensate, etc.
- Pulp and Paper industry — in digesters, in pumping green, white, and black liquors, light pulps, adding products such as kaolin, titanium dioxide, etc.
- Steel and mining industry — in recovery, gas scrubbers, acid recirculation, etc
- Industry in general — in the textile industry, pharmaceuticals, pollution control, sanitation, dyeing, water cooling, condensate, acid recovery, circulation of galvanic and dyeing baths, gas washing, filter feeding, and numerous other industrial processes.
OMEL Original Parts and Technical Assistance
Get your pump repaired by the manufacturer!
By choosing OMEL’s after-sales service, you can count on the factory warranty, trained technicians, complete reports to diagnose the need for replacement parts, automated processes for manufacturing high-quality parts, and final performance tests to release pumps and instruments. With the safety, durability, and reliability of products repaired by OMEL, you will have excellent results in your industrial process and reduced operating costs.
Discover more OMEL products
OMEL offers a wide range of high-quality products for various applications. Products offered include centrifugal pumps, vacuum pumps, metering pumps, roots blowers, ring compressors, rotameters, vacuum systems, and pinch valves.
Advantages of purchasing OMEL equipment
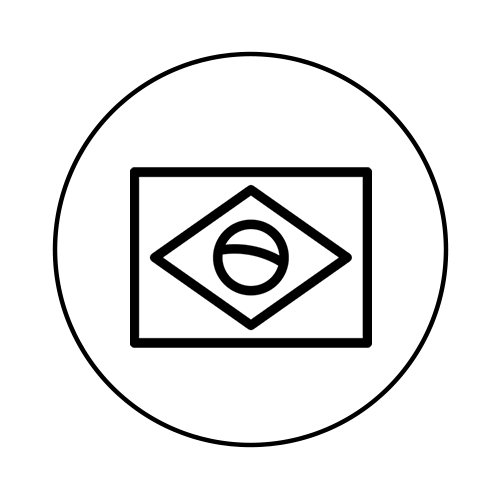
Fully national design and manufacturing
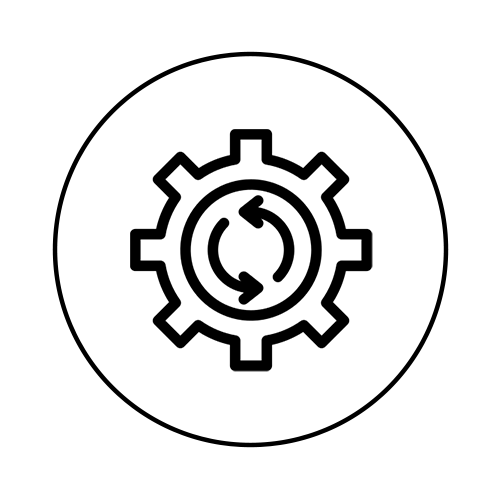
Original spare parts and ready delivery
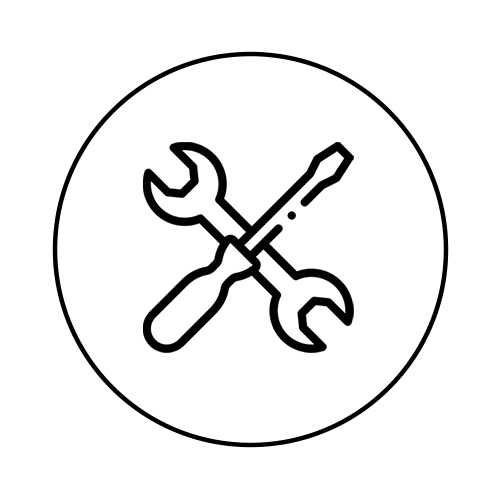
Specialized technical assistance
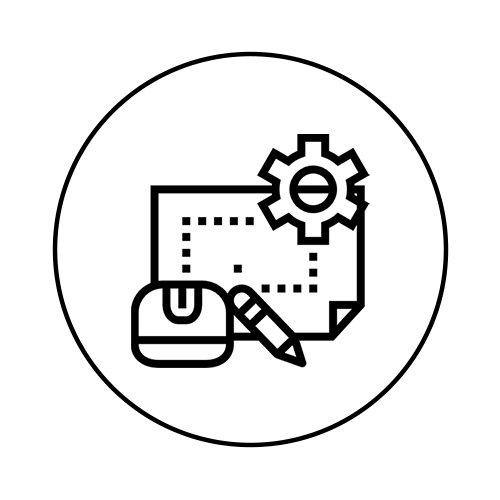
OMEL Engineering available to develop custom projects
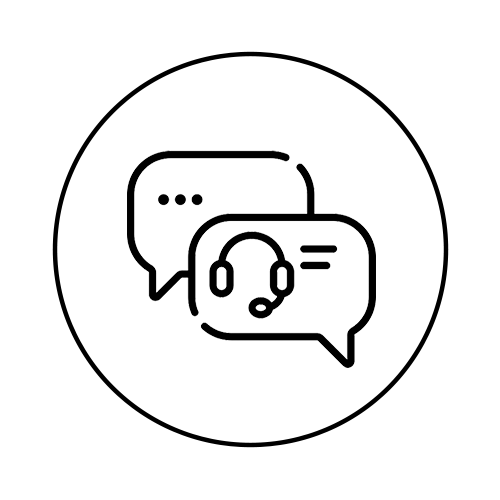
Technical support and online service
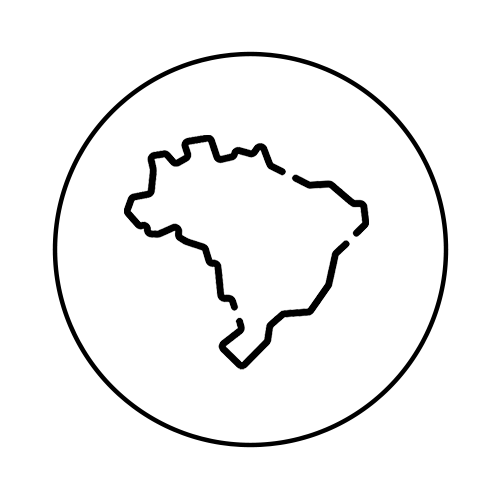
Service throughout the country

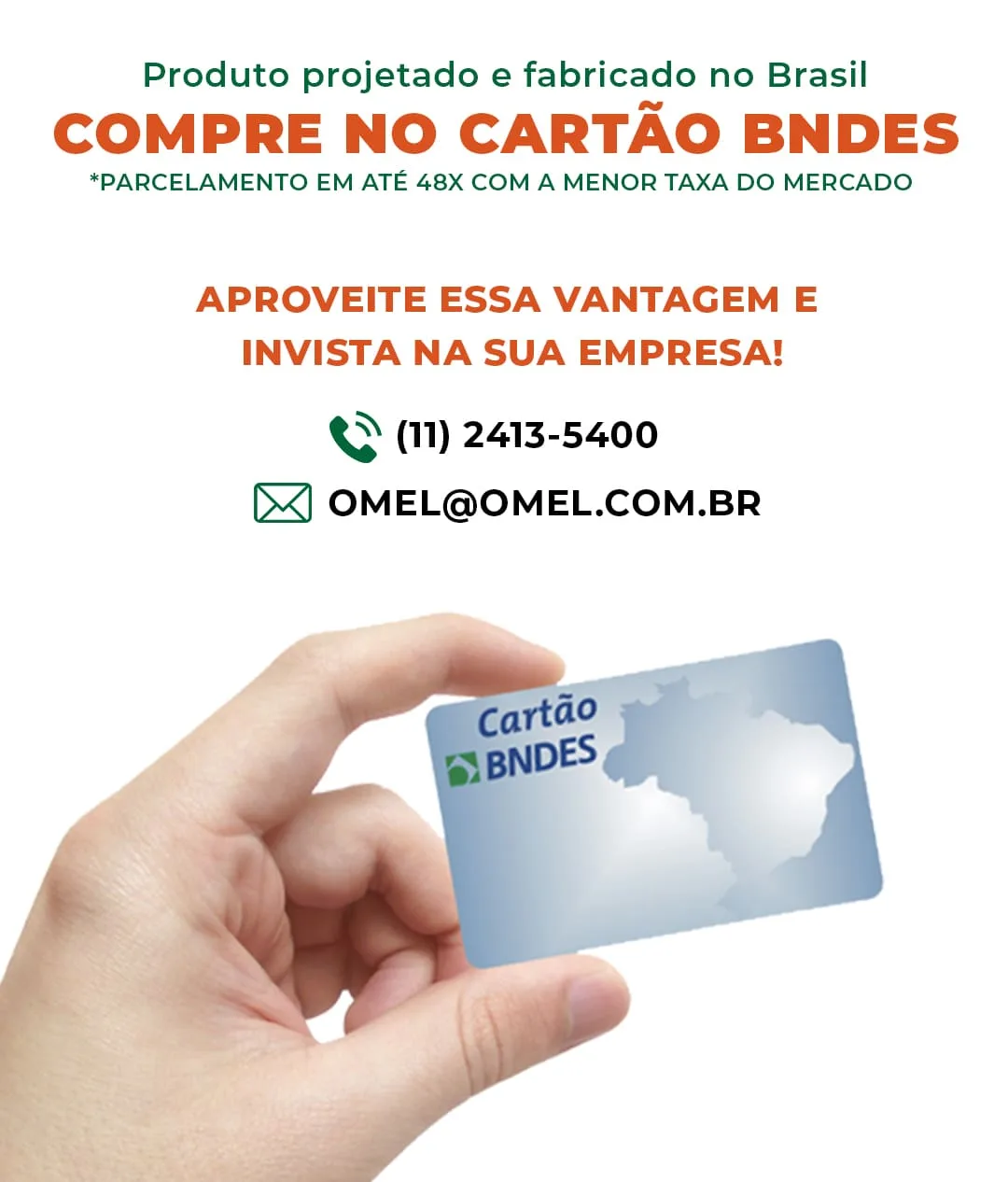